Unconventional Fitting Methods: A Revolution in Design and Manufacturing
In the ever-evolving world of design and manufacturing, unconventional fitting methods have begun to gain traction. These innovative approaches challenge the traditional norms and provide unique solutions to complex problems faced by engineers and designers.
What are Unconventional Fitting Methods?
Unconventional fitting methods refer to alternative techniques utilized for assembling components that deviate from traditional methods such as welding or screwing. These techniques often optimize performance, improve longevity, and reduce production times.
Some common examples include:
- Adhesive bonding: Utilizing specialized adhesives to bond surfaces together, eliminating the need for mechanical fasteners.
- Interference fitting: Using slightly oversized parts to create a tight fit through force.
- 3D-printed connectors: Custom manufacturing connectors that fit precisely with the components involved.
- Magnetic fittings: Employing magnets for easy assembly and disassembly without tools.
Why Choose Unconventional Fitting Methods?
There are several compelling reasons for adopting unconventional fitting methods in various applications:
- Cost-Effectiveness: While initial costs may be high for some unconventional methods, they often result in lower overall production costs due to reduced labor and material requirements.
- Time Savings: Many unconventional methods allow for faster assembly processes, reducing lead times and improving production schedules.
- Design Flexibility: These methods enable designers to create more complex shapes and assemblies without sacrificing strength or stability.
- Increased Strength and Durability: In some cases, unconventional fittings can provide superior strength compared to standard methods, resulting in longer-lasting products.
Comparison of Traditional vs. Unconventional Fitting Methods
Aspect | Traditional Methods | Unconventional Methods |
Assembly Time | Longer due to complex fastening processes | Shorter due to simplified assembly techniques |
Material Costs | Potentially higher from fasteners and tools | Can be lower utilizing adhesives or printed solutions |
Design Complexity | Restricted by traditional shapes | Enhanced flexibility allowing for innovative designs |
Strength | Varied, often dependent on fastener quality | May offer greater strength through seamless connections |
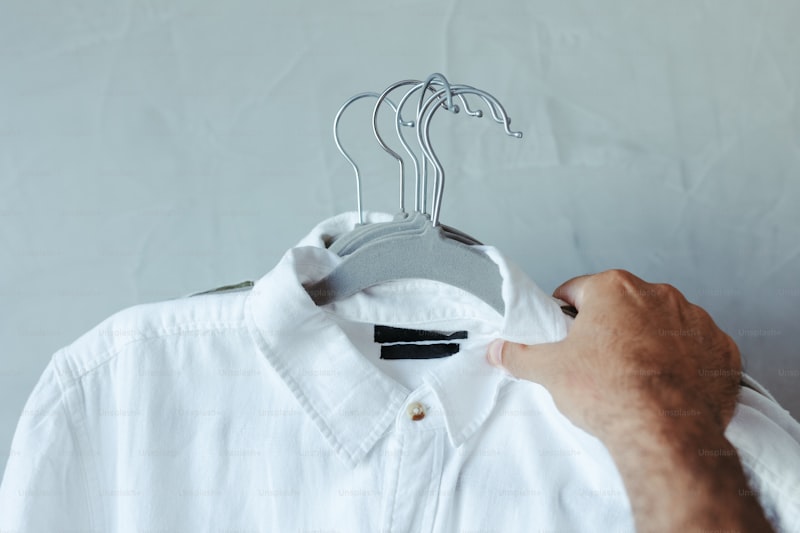
Applications of Unconventional Fitting Methods
Unconventional fitting methods are transforming various industries, including:
- Aerospace: Reduced weight and improved integrity of aircraft designs through the use of adhesive bonding and 3D printing.
- Automotive: Enhanced fuel efficiency and lower production costs with interference fittings and lightweight materials.
- Construction: Facilitated assembly of large structures using modular pieces that fit together seamlessly.
- Consumer Electronics: Sleek, modern designs utilizing magnetic fittings for user-friendly interfaces.
Challenges in Implementing Unconventional Fitting Methods
While there are numerous benefits, it’s essential to be aware of the challenges that may arise with the adoption of unconventional fitting methods:
- Training Requirements: Employees may require additional training to effectively use new methods and materials.
- Material Compatibility: Not all materials are suitable for every unconventional fitting method, requiring thorough investigation.
- Regulatory Standards: Compliance with safety and quality standards must be ensured for unconventional methods.
Tips for Selecting the Right Unconventional Fitting Method
When considering unconventional fitting methods for your project, keep the following tips in mind:
- Project Requirements: Assess the specific needs and constraints of your project, including load requirements and environmental factors.
- Material Selection: Choose materials that are compatible with the selected fitting method to ensure maximum performance.
- Prototype Testing: Create prototypes to test the effectiveness of the chosen fitting method before full-scale production.
- Consult Experts: Engage with professionals who specialize in unconventional methods to gain insights and recommendations.
Conclusion
In conclusion, unconventional fitting methods present exciting opportunities for innovation in design and manufacturing. By understanding the various techniques available, along with their benefits and challenges, companies can make informed decisions that lead to enhanced product performance and efficiency. As industries continue to evolve, staying abreast of these unconventional methods could be pivotal in maintaining a competitive edge.
Remember to carefully consider your project requirements, select appropriate materials, and involve experts when exploring unconventional fitting methods. This approach will maximize the potential of your designs while ensuring safety and quality in production.